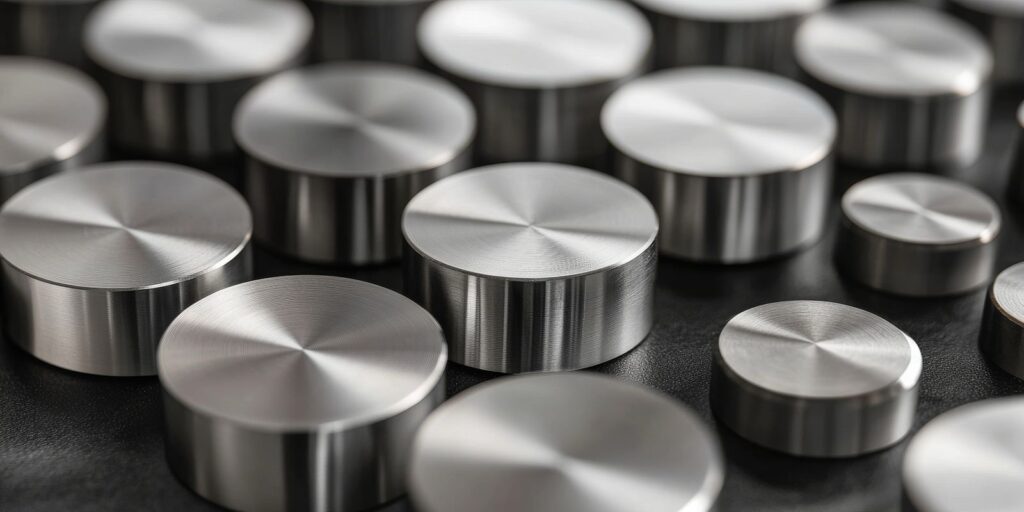
Aerospace engineers are today facing the challenge of designing aircraft and spacecraft that can lift immense loads, enduring extreme forces, and withstanding significant temperature fluctuations. For over a hundred years, engineers have used advanced metals, continually developing stronger, lighter aluminum and titanium alloys that have been the foundation of many iconic vehicles. Nonetheless, pioneering companies recently began moving toward smarter composite materials rather than metals, launching aerospace in an exciting new direction.
The Shift from Metal to Composite Materials
Aerospace engineers select building materials based on strength, stiffness, durability and lightness since every additional pound adds fuel costs across thousands of flights. Metals form incredibly strong structures but have limitations that aircraft are pushing up against, like thermal expansion issues at supersonic speeds. Furthermore, minor corrosion forces expensive teardowns of entire metal components instead of spot repairs.
New composite materials transform aerospace design by optimizing each property far beyond metals. Made by embedding fibers like boron, carbon or glass into plastic-like resins, they combine strengths like stiffness from the fibers with durability from the matrix. Each performs uniquely based on constituent ingredients, which are key for customization. Critically, composites resist corrosion and keep flying after damage that would ground metal builds. Their game-changing capacity lets aerospace push past prior constraints towards expansive new frontiers.
Customizing Materials to Demands with Aerospace Composites
Composite technology empowers aerospace engineers to move far past one-size-fits-all builds, instead tailoring unique materials precisely matched to design loads and local demands across individual components. Like reinforcing only high-stress areas, applying ideal resins to exposed leading wing edges while utilizing separate matrices internally. Such bespoke engineering maximizes performance while eliminating any unnecessary weight.
Specific composite formulations now exist for almost every aerospace application, from ultra-lightweight insulation foams that withstand searing reentry temperatures, to ultra-high rigidities supporting spacecraft structures. More broadly, engineers at pioneering companies like Axiom Materials can request fully customized aerospace composites by precisely specifying mechanical, thermal and chemical needs within tiny tolerances so chemists can formulate the exact required precursors. Such made-to-order refinement remains impossible in metals, demonstrating the greater design freedom composites confer.
Benefits Driving Adoption Across Industry Applications
Recent exponential expansions have resulted from the overwhelming advantages over incumbent metal builds that substantially improve vehicle performance, economics and longevity across applications.
Military aviation utilizes massive radar-evading shapes only possible with composites, reducing reflected signals for stealth while enabling larger internal payloads. Missiles switch from metal skins that expand unequally over composite casings maintaining precise aerodynamic profiles across extreme thermal ranges. Economy seating squeezes tighter pitches through composite frames meeting safety rules at lighter weights.
Such interconnected benefits drive booming demand as researchers uncover new high-performance materials and engineers better grasp how tailoring their structural layouts extracts maximum advantage. Soon, these smarter composites will fully supersede traditional aerospace metals.
The Most Exciting Future in Aerospace
Aerospace composites represent the most promising advancement in structural engineering since the dawn of flight, conferring unmatched flexibility to customize mechanical, thermal, and electrical performance. Their benefits expand yearly as pioneering companies incorporate more innovative formulations tailored to unlock greater vehicle capabilities across every operating regime. Expect multiplying adoption to transform flying machines as wholly metal builds fade into history, with smarter composites propelling all future progress.
Conclusion
After over a century building aircraft and spacecraft backbones from ever-improving metals, aerospace now shifts towards composites; tailored smart materials chemically formulated to precise needs. Composites optimize distinct mechanical and thermal properties between components in ways impossible with metals, enabling expansive performance gains. With its rapid adoption across the aerospace industry, the future of composites looks bright, promising decades of progress with vehicles that surpass the limitations of metal.